Body Bucks are a tradition way of automotive coachwork. Craftsman would create a buck from wood and wireforms and then hand build the panels around these forms. By using 3D Scanning we can create bucks for a builder to replicate these cars. These bucks can also be used as insurance for cars in the event of damage a replication part can be built from a body buck that exactly matches the vehicle to the highest degree of accuracy.
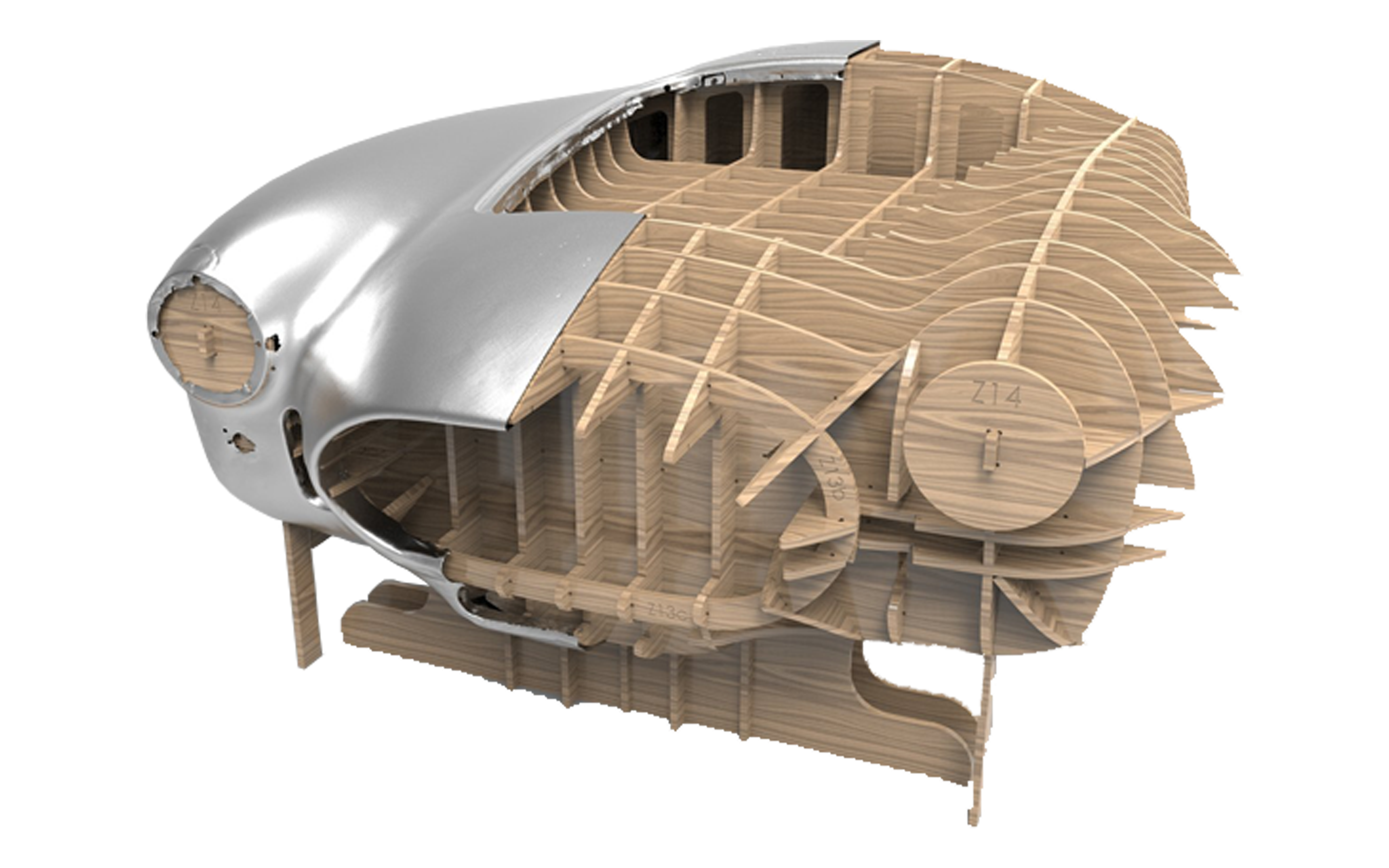
History Reimagined
Scan & Build
Coach building like the Masters
Building a car from a wooden buck and hammer formers has been around since the golden age of the first hand built Ferraris.
Today this lost art is bring reborn as metal craftsmen shape flat stocks into beautiful works of art. This process starts with the body buck and these bucks can now be created with great accuracy using 3D scanning, modelling, and CNC router technologies.
Not only are these used to recreate iconic cars of the past, but also as insurance archives for highly customized and vintage race cars. In the event of an accident, hand built panels can be recreated with pin point accuracy.
Our Process to Build a Body Buck

Plan and Scan
We plan out the project together to determine what needs to be 3D scanned.
All projects are different. From scanning a single fender to build a buck for to scanning an entire car, we need to discuss what is required and the state of the project. Environment is also important for the best scan possible. Indoors is required and highly reflective surfaces will require a removable paint film or marker dots be applied to scan properly. All of these details are discussed in our initial meetings prior to scanning the part of vehicle.

Design
We design the body buck and any customized areas of the body.
This is generally the part of the process that can take some time. We need to take the 3D scanned data and convert it into proper solid objects with the material thickness of the body panels. We also account for any customizations that may be required to the body design. These are then mapped to an internal body buck structure. These structures are finally sliced into parts on standard sized MDF sheets for a CNC Router to cut.

Refine
We work iteratively with you and your team to ensure the best design and fit.
Prior to getting things cut on a CNC Router, we will review all of the designs of the scanned body and buck to ensure they will work with you. In some cases we can even print scale models on our 3D printers to confirm any designs ahead of time. Once we have an agreed model, it is off to the CNC router to cut some wood!

Build
The final body buck is delivered and ready to be assembled by your team for coach work to begin.
This is where it gets really fun. The panels will be delivered by the CNC router company in cut and numbered panels. Using the 3D design mockups as design instructutions, each of these pieces are assembled according to the rendering and your team can start forming the sheet metal or aluminum to build someones dream car!