Developing a chassis for a hot rod or custom car has generally been a process of measuring by hand using various tools followed by paper planning and some trial and error in fabrication. By using 3D Scanning we can create accurate 3D models of an original chassis to 0.1mm accuracy. In addition the removed body and powertrain can also be 3D scanned to create exact models. These models can be used by chassis builders to create a custom chassis that matches the vehicle to the highest degree of accuracy and ensures operation and clearance of mechanical components.
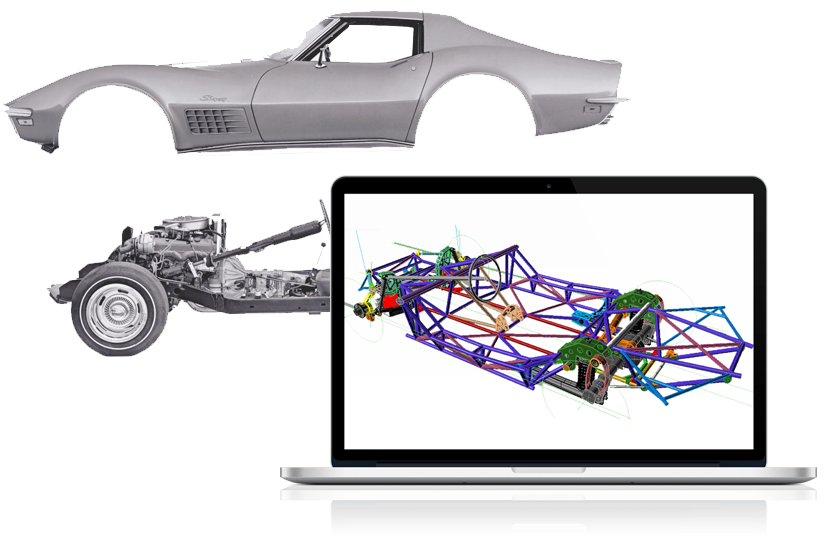
Process Refined
Precision Matters
Making the Old Fit the New
Traditional ways of measuring a classic car chassis have worked, but are risky. Creating an accurate measurement requires doing it on a completely level surface, having tools that are precise and calibrated, and checking multiple times to ensure the correct reading was made. Even with multiple checks, these methods have human error that can cause incorrect measurements that impact a chassis design.
In addition, trying to make sure that a body will fit correcly and that the engine and trasmission will clear all the required components introduces more measuring and in some cases corrections to the chassis late in the process.
3D Scanning of a chassis and body can be done with precsision between 0.04mm and 0.1mm when precision truly matters.
3D Development allows for the creation of a chassis in a virtual space that will ensure that body fits, the suspension components will clear, and the powertrain will fit all before welding a single piece.
These models can then be precision cut with CNC plasma and waterjet tables and welded together to make a compete and accurate custom chassis.
Our Process to Build a Body Buck

Plan and Scan
We plan out the project together to determine what needs to be 3D scanned.
All projects are different. From scanning a single engine to doing the frame, body, and full powertrain – we discuss what is required for the project. Environment is also important for the best scan possible. Indoors is required and highly reflective surfaces will require a removable paint film or marker dots be applied to scan properly. In addition, the frame needs to be apart from the body and the body can be scanned on a hoist or rotisserie to get underneath. All of these details are discussed in our initial meetings prior to scanning the part of vehicle.

Design
The design of your customized chassis to perfectly fit your build.
This is generally the part of the process that can take some time. We need to take the 3D scanned data and convert it into proper solid objects. We have chassis designers that we can work with to create a chassis that you are looking for, or we can work with your team / designer to get them the models they need to design your chassis.

Refine
We work iteratively with you and your team to ensure the best design and fit.
We will work with your team / designer to refine any models as needed or to get more 3D scans as necessary. If working with our chassis designers, this is also the stage where any revisions or changes are discussed such as wheel choices, suspension types, etc.

Build
The final chassis is sent for cutting and assembly.
This is where it gets really fun. The finalized chassis designs from either or designers or your team are sectioned to be cut on a CNC plasma and/or water jet table. From there the individual pieces are then assembled by your fabrication department to build the ultimate custom chassis!